CASE STUDY
Graymont’s new Kiln 2 dust extractor plays a key role in its environmental care policy
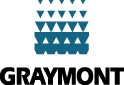
Sustainability and environmental care are a key focus of Graymont, and DUSTEX was briefed to design a dust extractor that reduces air emissions, improves energy efficiency, and reduces waste.
Background:
Graymont is a global leader in the supply of lime and limestone products through the USA, Canada, and Asia-Pacific. Graymont approached DUSTEX to undertake a study and design to replace an existing wet scrubber filtration system with a dry bag filter. The dust extractor is for filtering calcium oxide dust from a rotary kiln at their plant in Otorohanga, Waikato.
The problem:
Graymont’s existing wet scrubber filtration system was labour and land intensive because the sludge had to be extracted from settling ponds and transported away for disposal. It is also a lost opportunity to re-use materials.
Sustainability and environmental care are a key focus of Graymont’s HSE Management System: the pillars of this are air emissions, energy efficiency, and waste reduction. DUSTEX’s brief was to deliver a system that provided significant improvements in all of these areas. The new dust extractor needed to decrease dust and fume emissions into the air, and allow the dust collected to be reused.
The solution:
DUSTEX designed the entire new dust collection system, ID fan, and bag filter system, working with JP Marshall Engineering. JP Marshall engineering designed and supplied the mechanical handling equipment. They completed final fabrication design and drawings for support towers, access stairs and general plant arrangement and provided an in depth end to end service.
DUSTEX also assisted Graymont with the building consent approvals to build the new dust extractor.
Some highlights of the new industrial dust collector designed by DUSTEX:
- The entire dust collection system is 16m tall, 8m long, and 11m wide.
- The dust collector comprises1056 x ø153 x 4m fiberglass with PTFE laminate membrane filter bags, operating at 250°C.
- The system incorporates an air tempering damper valve using an electric actuator in the extraction ducting to reduce the kiln off gas temperatures and protect the filter bags from excessive air temperatures that would cause damage.
- The dust extractor was entirely fabricated from 304 stainless steel with 100mm thick insulation and cladding.
- Extraction ducting was made from Mild steel, and the clean air ducting was manufactured from 304 stainless steel.
- The ID fan is capable of moving over 30Am³/s at 250°C and made use of the existing 500kW 4-pole motor.
- The materials handling system comprises double flap valves, screw conveyors, and a bucket elevator. The dust from the dust extraction system is able to move to the silo at a rate of 4.8 tons of dust per hour.
- The dust collector hopper is heated to prevent condensation inside the collector during shutdown periods.
- The dust extractor pulsing cleaning system is an on-demand, on-line cleaning system.
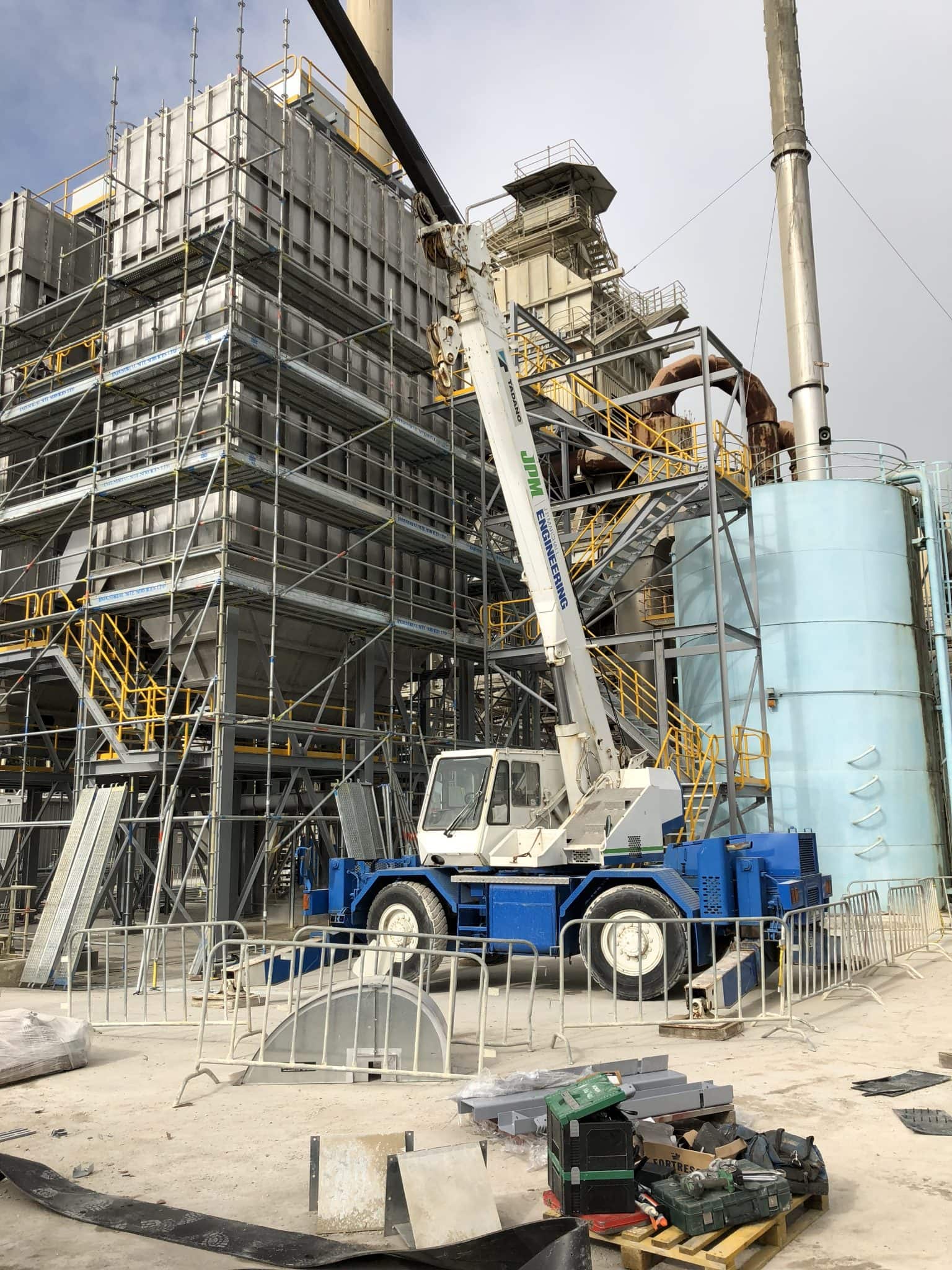