CASE STUDY
Winstone Wallboards’ bin vent dust collector increased efficiency and reduced maintenance time

Manufacturing GIB® plasterboard means that there’s a lot of plaster dust in the air. Winstone Wallboards needed to replace an unreliable and inefficient dust collector, and the new bin vent dust collector designed and manufactured by DUSTEX also reduced maintenance time by 20%.
Background:
In the process of manufacturing GIB® plasterboard, bulk powdered plaster is conveyed into large (55 and 90 ton) bins prior to mixing, through a dilute phase conveying system.
The problem:
Two existing dust collectors, one on stand-by, were used to filter out the plaster dust from the conveying air.
However, the existing dust collectors were inefficient, prone to mechanical failure, and costly to maintain.
Winstone Wallboards Ltd sought proposals to replace one of the existing dust collectors with the objectives of eliminating excess dust generation; preventing further mechanical failure; reducing filter bag wear; ensuring workspace environment compliance; and reducing maintenance cost. The unit also needed to be designed around certain physical constraints to avoid the cost of relocating other equipment.
The solution:
DUSTEX designed a bin vent dust collector specifically for the expected airflow and dust load meeting all Winstone Wallboards’ objectives.
The new bin vent is much easier to maintain and the time taken to service the new bin vent has been reduced to about 20% of that of the old unit.
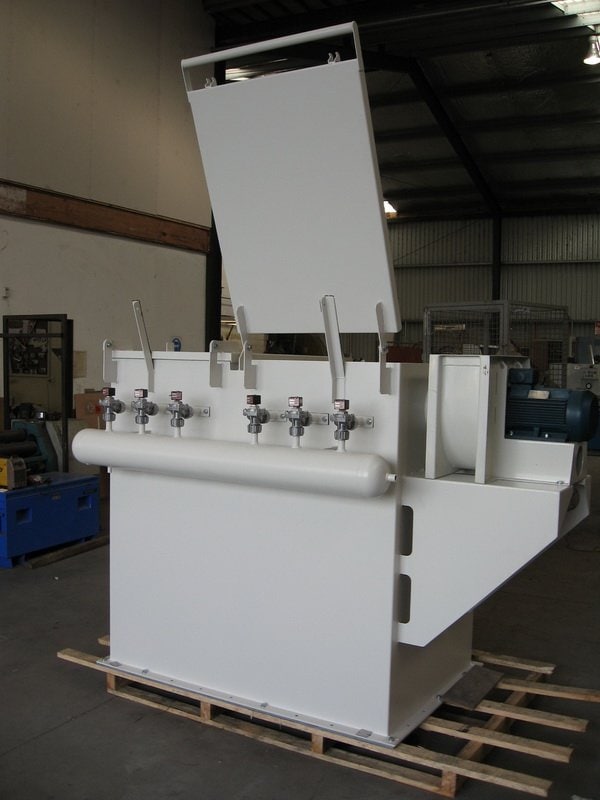